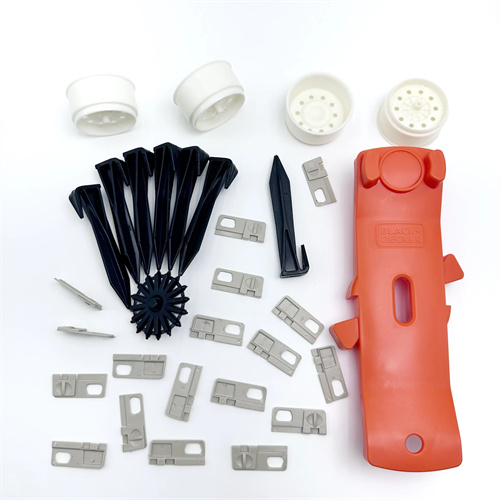
Custom Injection Molded Parts
Tailored Design: Custom injection molded parts are designed to precisely fit the specific needs of a particular product or application. This could involve unique shapes, sizes, functional features, or aesthetic requirements. For example, in LED lighting, custom parts might be designed to optimize light distribution or heat dissipation.
High Precision: The injection molding process allows for a high degree of precision and accuracy in manufacturing. Custom parts can be produced with tight tolerances, ensuring consistent quality and proper fit within the final product. In electronics and electrical appliances, this precision is crucial for components to function properly and integrate seamlessly.
Material Selection Flexibility: A wide range of plastic materials can be used in custom injection molding. Different materials offer various properties such as strength, durability, heat resistance, electrical insulation, and transparency. For packaging applications, materials can be chosen for their barrier properties to protect the contents.
Custom Injection Molded Parts refer to plastic components that are specifically designed and manufactured through the injection molding process to meet unique requirements and specifications of various industries such as LED Lighting, Electronics, Electrical Appliances, and Packaging.
Manufacturing Process of Custom Injection Molded Parts
Design and Engineering: The process begins with detailed design and engineering. Engineers work with customers to understand their requirements and create 3D models and detailed drawings of the custom parts. Computer-aided design (CAD) and computer-aided engineering (CAE) software are used to optimize the design for manufacturability and performance.
Mold Making: Once the design is finalized, a mold is created. The mold is a crucial tool that determines the shape and features of the custom part. It is typically made of steel or aluminum and is manufactured with high precision using techniques like CNC machining. The complexity of the mold depends on the design of the part; for multi-shot injection molded parts, the mold is more intricate, allowing for the combination of different materials or colors in a single part.
Injection Molding: The plastic material, in the form of pellets, is fed into an injection molding machine. The machine heats the pellets until they become a molten liquid and then injects the molten plastic into the mold cavity under high pressure. The plastic fills the cavity and takes the shape of the mold. After a period of cooling and solidification, the mold opens, and the custom part is ejected.
Quality Inspection: After production, the custom injection molded parts undergo rigorous quality inspection. This includes checking for dimensional accuracy, surface finish, and any defects such as cracks, warping, or voids. Quality control measures ensure that the parts meet the specified standards and requirements.
Applications of Custom Injection Molded Parts
LED Lighting: Custom injection molded parts are used to create various components in LED lighting systems. This includes light diffusers, which are designed to evenly distribute light and enhance the visual effect. Heat sinks made from custom injection molded plastics can also help dissipate heat generated by the LEDs, improving the lifespan and performance of the lighting products.
Electronics: In the electronics industry, custom injection molded parts are widely used for components such as connectors, housings for electronic devices, and circuit board mounts. These parts need to have precise dimensions to ensure proper connection and protection of electronic components. They can also be designed with features like electromagnetic shielding to prevent interference.
Electrical Appliances: For electrical appliances, custom injection molded parts play an important role in the production of outer shells, control panels, and internal components. The shells can be designed to be aesthetically pleasing, durable, and easy to clean. Control panels can be molded with integrated buttons and displays for user convenience.
Packaging: Custom injection molded parts are used in packaging applications to create containers, closures, and other packaging components. They can be designed to have specific shapes and sizes to fit different products, and materials can be selected to provide protection, tamper resistance, and ease of use. For example, custom injection molded caps and lids can have unique designs for better sealing and opening.
Advantages of Custom Injection Molded Parts
Cost-Effective in High-Volume Production: Although the initial investment in mold making and setup may be high, for high-volume production, custom injection molded parts offer significant cost savings. The production process is highly efficient, allowing for the rapid and consistent production of a large number of parts, reducing the per-unit cost.
Enhanced Product Performance: By customizing the design and materials, the performance of the final product can be greatly enhanced. The parts can be optimized for specific functions, such as improving heat resistance in electronics or increasing the strength of packaging containers.
Brand Differentiation: Custom injection molded parts can help companies achieve brand differentiation. Unique designs and features can make their products stand out in the market, attracting more customers and increasing brand value.
Challenges of Custom Injection Molded Parts
Design Complexity: Highly complex custom designs may require more advanced mold-making techniques and longer production times. It’s important to balance design requirements with manufacturability to avoid delays and cost overruns.
Material Compatibility: When using multi-shot injection molding or combining different materials in a custom part, ensuring material compatibility is crucial. Incompatible materials can lead to issues such as poor adhesion or warping.
Tooling Costs: The cost of creating custom molds can be significant, especially for complex parts. Companies need to carefully consider the production volume and return on investment before deciding to produce custom injection molded parts.