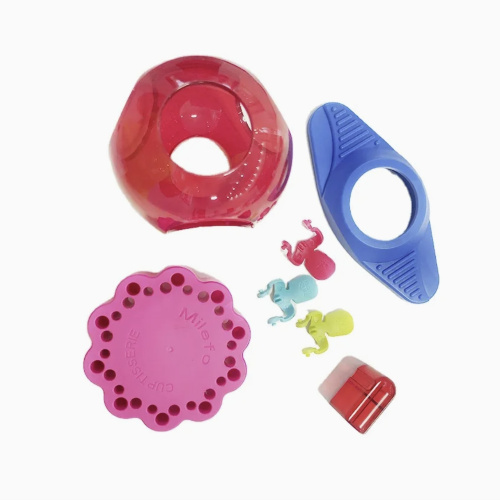
High-Volume Injection Molded Parts:
As a leading manufacturer, we have mastered the art and science of producing high-volume injection molded parts, catering to the diverse needs of industries such as home appliances, hardware tools, medical devices, and sports goods. High-volume injection molded parts play a pivotal role in these sectors, enabling the mass production of high-quality components at an optimal cost.
In today’s competitive manufacturing landscape, the ability to produce large quantities of parts efficiently is crucial. High-volume injection molded parts offer several advantages. Firstly, they provide cost-effectiveness. The injection molding process, when scaled for high-volume production, allows for significant economies of scale. The initial investment in tooling and equipment is spread over a large number of parts, reducing the per-unit cost. Secondly, it ensures consistent quality. Once the injection molding process is optimized, each part produced is virtually identical in terms of dimensions, material properties, and surface finish. This consistency is vital for industries where precision and reliability are non-negotiable, such as medical devices and hardware tools.
Manufacturing Process for High-Volume Injection Molded Parts
Design and Tooling
The journey of high-volume injection molded parts begins with meticulous design. Our team of experienced engineers uses advanced computer-aided design (CAD) software to create detailed 3D models of the parts. When designing for the home appliances industry, for example, we consider factors like ergonomics, functionality, and aesthetic appeal. In the case of medical devices, biocompatibility, sterilizability, and precision are at the forefront of the design process.
Once the design is finalized, the tooling phase commences. High-volume production requires molds that are robust and durable. We use high-quality steel or aluminum to fabricate molds, often with multiple cavities. Multi-cavity molds allow us to produce several parts in a single injection cycle, significantly increasing production efficiency. For hardware tools, where parts are often small and simple in shape, multi-cavity molds can be designed to produce dozens of parts at once.
Material Selection
Choosing the right plastic material is crucial for high-volume injection molded parts. In the home appliances industry, materials like acrylonitrile butadiene styrene (ABS) and polypropylene (PP) are commonly used. ABS offers good impact resistance and a high-quality surface finish, making it suitable for appliance housings. PP, on the other hand, is lightweight, chemically resistant, and cost-effective, making it ideal for components like handles and internal parts.
For medical devices, biocompatible materials such as medical-grade silicone, polyethylene terephthalate (PET), and polycarbonate (PC) are preferred. These materials must meet strict regulatory standards to ensure patient safety. In the sports goods industry, materials like high-density polyethylene (HDPE) and ethylene-vinyl acetate (EVA) are used for their shock-absorbing and durable properties.
Injection Molding Process
Our state-of-the-art injection molding machines are the workhorses of high-volume production. Plastic pellets are fed into the machine’s hopper and heated to a molten state. The molten plastic is then injected into the mold cavity under high pressure. The pressure ensures that the plastic fills every intricate detail of the mold, accurately replicating the design. After injection, the plastic cools and solidifies within the mold. The cooling time is carefully controlled to ensure proper dimensional stability of the part.
For high-volume production, we often use high-speed injection molding machines that can cycle quickly, reducing the time between each injection. This, combined with the use of multi-cavity molds, allows us to produce a large number of parts in a short period.
Quality Control
Quality control is an integral part of the high-volume injection molding process. We have implemented a rigorous quality management system to ensure that each part meets the highest standards. Every part undergoes inspection for dimensional accuracy, surface finish, and structural integrity. In the medical device industry, additional tests are performed to ensure biocompatibility and sterility.
We use automated inspection systems for high-volume production to speed up the quality control process. These systems can quickly detect any defects, such as cracks, warping, or incorrect dimensions. Defective parts are immediately removed from the production line, preventing them from reaching the end-customer.
Applications of High-Volume Injection Molded Parts
Home Appliances
In the home appliances industry, high-volume injection molded parts are used in a wide range of products. Appliance housings, such as those for refrigerators, washing machines, and microwave ovens, are often made through high-volume injection molding. These housings not only protect the internal components but also contribute to the aesthetic appeal of the appliance. Control panels, knobs, and handles are also injection molded in large quantities. For example, the plastic knobs on a stove are produced in high volumes to ensure consistency in appearance and functionality across all units.
Hardware Tools
Hardware tools rely heavily on high-volume injection molded parts. The handles of screwdrivers, pliers, and hammers are often injection molded from materials like rubber-coated plastics or soft-touch polymers to provide a comfortable grip. Tool housings, such as those for power drills and circular saws, are also made through injection molding. These housings protect the internal components and provide a durable and ergonomic exterior. Small internal components, like gears and clips, are produced in high volumes to meet the demands of the hardware tool market.
Medical Devices
In the medical device industry, high-volume injection molded parts are used in the production of a variety of products. Disposable syringes, catheters, and blood collection tubes are all made through high-volume injection molding. These parts must be produced with the utmost precision and quality to ensure patient safety. In addition, components for more complex medical devices, such as surgical instruments and diagnostic equipment, are also injection molded in large quantities. For example, the plastic components of a laparoscopic surgical instrument are produced in high volumes to meet the demand for minimally invasive surgery.
Sports Goods
The sports goods industry benefits greatly from high-volume injection molded parts. Protective gear, such as helmets, knee pads, and elbow pads, are often made from injection molded plastics. These parts are designed to provide maximum protection while being lightweight and comfortable. In addition, sports equipment like golf club heads, tennis racket frames, and bicycle seats are produced through high-volume injection molding. The ability to produce these parts in large quantities allows for cost-effective manufacturing, making sports goods more accessible to consumers.
Multi-Shot Injection Molding in High-Volume Production
Multi-shot injection molding can also be incorporated into high-volume production processes for added functionality and design flexibility. In the home appliances industry, multi-shot injection molding can be used to create components with soft-touch grips or to combine different materials for improved performance. For example, a blender handle can be molded with a hard plastic core for strength and a soft-touch outer layer for comfort.
In the sports goods industry, multi-shot injection molding can be used to create parts with different colored sections or to combine materials with different properties. For example, a running shoe sole can be molded with a hard outer layer for durability and a soft inner layer for shock absorption.
As a manufacturer, our expertise in producing high-volume injection molded parts has allowed us to meet the demands of industries such as home appliances, hardware tools, medical devices, and sports goods. By leveraging advanced manufacturing processes, quality control measures, and innovative techniques like multi-shot injection molding, we are able to provide our customers with high-quality parts at a competitive price.