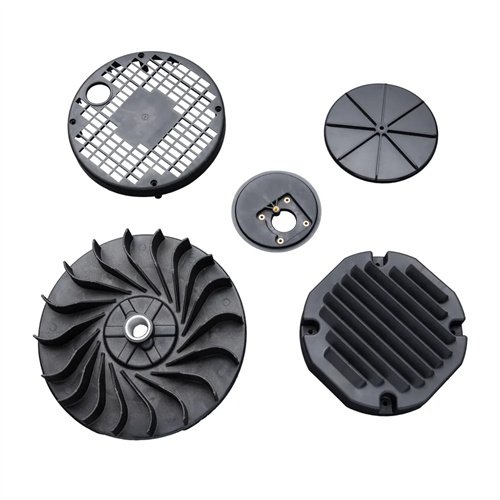
Injection Molded Plastics
As a leading manufacturer, we are at the forefront of harnessing the power of injection molded plastics to create high – quality products across a wide spectrum of industries, including medical devices, sports goods, LED lighting, and electronics. Injection molded plastics have become an integral part of modern manufacturing due to their versatility, precision, and cost – effectiveness.
Injection molded plastics start their journey as plastic resins, usually in the form of small pellets. These resins are carefully selected based on their inherent properties, such as strength, flexibility, heat resistance, chemical resistance, and transparency. Once chosen, they are fed into a highly sophisticated injection molding machine.
The injection molding machine heats the plastic pellets until they transform into a molten, flowable state. Under high pressure, this molten plastic is forcefully injected into a pre – designed mold cavity. The mold cavity is crafted with extreme precision to impart the desired shape to the plastic. After filling the cavity, the plastic cools and solidifies, taking on the exact form of the mold. This results in the creation of injection molded plastic components with exceptional dimensional accuracy and a smooth surface finish.
Types of Injection Molded Plastics
Thermoplastics
Thermoplastics are the most commonly used type of plastics in injection molding. They can be repeatedly heated and cooled, allowing for multiple shaping processes. Examples include polyethylene (PE), polypropylene (PP), polystyrene (PS), acrylonitrile – butadiene – styrene (ABS), and polycarbonate (PC). In the electronics industry, ABS is widely used for its good mechanical properties and ease of processing. It is often employed in the production of electronic device housings, providing durability and a sleek appearance.
Engineering Plastics
Engineering plastics are a specialized class of thermoplastics with enhanced performance characteristics. Nylon, for instance, is highly regarded for its high strength, wear resistance, and low friction properties. In the medical device industry, nylon can be used to manufacture components such as gears in surgical instruments. Polyetheretherketone (PEEK) is another engineering plastic known for its excellent heat resistance, chemical resistance, and biocompatibility. It is increasingly used in medical implants and high – performance electronic components.
Manufacturing Process of Injection Molded Plastics
Material Selection
Our manufacturing process begins with a meticulous material selection phase. When catering to the medical device industry, biocompatibility and sterilizability are of utmost importance. We choose plastics that meet strict regulatory standards, such as medical – grade silicone and polypropylene. In the sports goods industry, materials are selected based on their ability to withstand high – impact forces, such as high – density polyethylene (HDPE) for protective sports equipment. For LED lighting and electronics, factors like electrical insulation properties and heat dissipation capabilities are considered.
Mold Design and Fabrication
The mold is the heart of the injection molding process. Our team of skilled engineers utilizes advanced computer – aided design (CAD) and computer – aided manufacturing (CAM) software to design molds that are customized to the specific requirements of each project. For high – volume injection molded parts, we design molds with multiple cavities to maximize production efficiency. In the electronics industry, where miniaturization is key, molds are designed to create components with extremely precise dimensions. Molds are fabricated from high – quality steel or aluminum using precision machining techniques to ensure long – term durability and accurate replication of the design.
Injection Molding
Once the material is selected and the mold is ready, the injection molding process commences. The plastic pellets are fed into the injection molding machine’s hopper. The machine heats the pellets to the appropriate temperature, which varies depending on the type of plastic. The molten plastic is then injected into the mold cavity at high pressure. The pressure ensures that the plastic fills every intricate detail of the mold, even in complex designs. After injection, the plastic cools and solidifies. The cooling time is carefully controlled to guarantee proper dimensional stability of the component. Different plastics have different cooling requirements, and our expertise allows us to optimize this process for each material.
Quality Control
Quality control is an essential part of our manufacturing process. Every injection molded plastic component undergoes rigorous inspection. We check for dimensional accuracy, surface finish, and any signs of defects such as voids, cracks, or warping. In the medical device industry, where product safety is critical, we perform additional tests to ensure biocompatibility and sterility. In the LED lighting industry, components are inspected for optical properties to ensure proper light transmission and diffusion. Only components that meet our stringent quality standards are approved for further processing or shipment.
Applications in Diverse Industries
Medical Devices
In the medical device industry, injection molded plastics play a crucial role. They are used in a wide range of applications, from disposable syringes and catheters to complex surgical instruments and medical implants. Disposable syringes are typically made from medical – grade polypropylene, which is lightweight, cost – effective, and can be easily sterilized. Catheters are often made from materials like polyurethane or silicone, which offer flexibility and biocompatibility. In the case of surgical instruments, injection molded plastic components can be used to create ergonomic handles and precise moving parts.
Sports Goods
The sports goods industry benefits greatly from injection molded plastics. Protective gear such as helmets, knee pads, and elbow pads are often made from materials like ABS or HDPE. These plastics provide excellent impact resistance, protecting athletes from injuries. In addition, sports equipment such as golf club heads, tennis racket frames, and bicycle seats are also made using injection molded plastics. These materials allow for the creation of lightweight yet strong components, enhancing the performance of the equipment.
LED Lighting
In the LED lighting industry, injection molded plastics are used for various components. Light diffusers, which are responsible for evenly distributing light, are often made from injection molded plastics with high light transmittance properties. These diffusers can be designed to create different lighting effects, such as soft white light or focused spotlights. Lamp housings are also made from injection molded plastics, providing protection for the LED components and contributing to the overall aesthetic of the lighting fixture. Some LED lighting products also use injection molded plastic heat sinks to dissipate heat generated by the LEDs, improving their lifespan and performance.
Electronics
In the electronics industry, injection molded plastics are everywhere. Electronic device housings, such as those for smartphones, tablets, and laptops, are commonly made from injection molded plastics. These housings not only protect the internal components but also contribute to the device’s aesthetics. Injection molded plastic components are also used for circuit board mounts, connectors, and switches. In addition, plastics with good electrical insulation properties are used to prevent short circuits and ensure the safe operation of electronic devices.
Multi – Shot Injection Molding and Injection Molded Plastics
Multi – shot injection molding is a specialized technique that we employ to create more complex and functional injection molded plastic components. In this process, multiple types of plastic materials or different colors of the same material are injected into the mold in sequential shots. In the electronics industry, multi – shot injection molding can be used to create components with soft – touch grips or to combine different materials for improved functionality. In the LED lighting industry, it can be used to create light diffusers with different optical properties in a single component. This technique reduces the need for additional assembly steps and allows for the creation of more innovative and efficient products.
As a manufacturer, our in – depth understanding of injection molded plastics, combined with our advanced manufacturing techniques and strict quality control, enables us to provide top – notch products to our clients in the medical devices, sports goods, LED lighting, and electronics industries. We are dedicated to continuously improving our processes and product offerings to meet the ever – evolving needs of these industries.