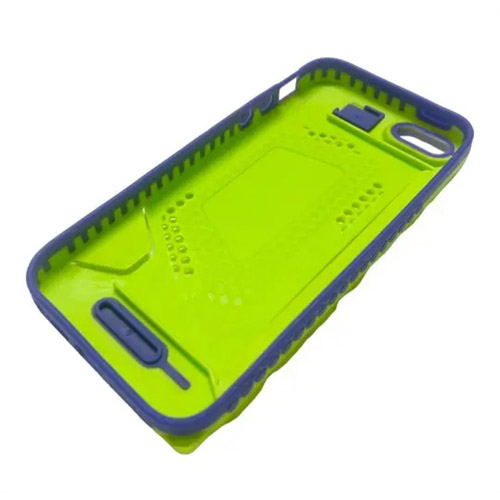
Multi – Shot Injection Molding
As a leading manufacturer, we are deeply involved in the utilization of advanced manufacturing techniques, with multi – shot injection molding standing out as a game – changer in the production of custom injection molded parts, high – volume injection molded parts, and injection molded components across various industries such as electrical appliances, packaging, construction, and toy.
Multi – shot injection molding is a sophisticated manufacturing process that goes beyond traditional injection molding. In a standard injection molding process, a single type of plastic material is injected into a mold cavity to form a component. However, multi – shot injection molding allows for the sequential injection of multiple types of plastic materials or different colors of the same material into a single mold cavity. This is achieved through the use of specialized injection molding machines equipped with multiple injection units and complex mold designs.
How It Works
The process begins with the design of a mold that can accommodate multiple injection steps. The mold is typically designed with movable cores and cavities that can be repositioned between injection shots. When the first shot of plastic is injected, it fills a specific part of the mold cavity and solidifies. Then, the mold is reconfigured, and a second shot of plastic, which can be a different material or color, is injected. This second shot bonds with the first shot, creating a single, integrated component with multiple material properties or colors. The process can be repeated for additional shots if required, depending on the complexity of the design.
Applications in Different Industries
Electrical Appliances
Enhanced Functionality
In the electrical appliances industry, multi – shot injection molding is used to create components with enhanced functionality. For example, in the production of appliance handles, a hard plastic can be used for the structural part of the handle to provide strength and durability, while a soft – touch plastic is injected in a subsequent shot to create a comfortable grip. This combination of materials not only improves the user experience but also increases the lifespan of the handle, as the hard plastic can withstand mechanical stress, and the soft – touch plastic reduces wear and tear from frequent use.
Aesthetic Appeal
Multi – shot injection molding also allows for the creation of aesthetically pleasing designs. Control panels for electrical appliances can be molded with different colored plastics to clearly distinguish between different functions. For instance, the power button on a microwave oven can be molded in a bright, attention – grabbing color, while the other function buttons are in a more subdued color, making it easier for users to operate the appliance.
Packaging
Tamper – Evident Features
In the packaging industry, multi – shot injection molding is used to create tamper – evident features. For example, bottle caps can be designed with an inner layer of plastic that seals the bottle and an outer layer that has a break – away strip. When the bottle is opened for the first time, the outer strip breaks, indicating that the product has been tampered with. This is achieved by injecting two different types of plastics in a multi – shot process, with the outer plastic being more brittle and designed to break easily.
Improved Barrier Properties
Multi – shot injection molding can also be used to improve the barrier properties of packaging. For products that require protection from moisture, oxygen, or other environmental factors, a multi – layer structure can be created. For example, a food packaging container can be molded with an inner layer of a plastic with good barrier properties, such as ethylene – vinyl alcohol copolymer (EVOH), and an outer layer of a more durable and cost – effective plastic like polyethylene. This combination provides both protection for the product and cost – effectiveness in production.
Construction
Structural Integrity and Aesthetics
In the construction industry, multi – shot injection molding is used to create components with both structural integrity and aesthetic appeal. For example, plastic window frames can be molded with a core of a strong, rigid plastic for structural support and an outer layer of a plastic with a different color or texture for a more attractive appearance. This not only enhances the durability of the window frame but also allows for greater design flexibility, as different colors and finishes can be achieved without the need for additional painting or finishing processes.
Weather Resistance
Multi – shot injection molding can also be used to create components with enhanced weather resistance. For outdoor applications, such as plastic fencing or decking components, a multi – layer structure can be created. The inner layer can be a plastic with high strength and impact resistance, while the outer layer can be a plastic with UV – resistant properties. This protects the inner layer from the damaging effects of sunlight and extends the lifespan of the component.
Toy
Innovative Designs
The toy industry benefits greatly from multi – shot injection molding in terms of innovative designs. Toys can be created with different colored parts or parts made from materials with different textures in a single molding process. For example, a toy car can be molded with a hard plastic body for durability and a soft – touch plastic for the wheels, providing a better grip on various surfaces. This not only makes the toy more functional but also more visually appealing to children.
Safety and Durability
Multi – shot injection molding can also improve the safety and durability of toys. By using different materials in different parts of the toy, manufacturers can ensure that the toy is safe for children to play with. For example, the edges of a toy can be molded with a softer plastic to prevent injury, while the main body of the toy is made from a more durable plastic to withstand rough play.
Advantages of Multi – Shot Injection Molding for Manufacturers
Cost – Effectiveness in the Long Run
Although the initial investment in multi – shot injection molding equipment and mold design is higher compared to traditional injection molding, in the long run, it can be more cost – effective. By creating components with multiple functions or colors in a single molding process, the need for additional assembly steps and secondary operations is reduced. This saves both time and labor costs, making it an attractive option for high – volume production.
Design Flexibility
Multi – shot injection molding offers unparalleled design flexibility. Manufacturers can create components with complex geometries, multiple material properties, and different colors, allowing them to meet the specific requirements of different industries. This flexibility also enables the development of innovative products that can stand out in the market.
Quality and Consistency
The process ensures high quality and consistency in the production of components. Since the multiple shots of plastic are integrated during the molding process, the bond between the different materials is strong and reliable. This results in components with fewer defects and a longer lifespan, which is crucial for industries such as electrical appliances and construction.
As a manufacturer, our adoption of multi – shot injection molding has enabled us to provide high – quality, innovative injection molded components to industries such as electrical appliances, packaging, construction, and toy. The versatility and advantages of this advanced manufacturing technique position us well to meet the evolving needs of our customers and contribute to the growth and innovation in these industries.